Maintenance is an essential aspect of machine manufacturing.
It involves various activities aimed at preserving and improving equipment’s performance, reliability, and lifespan.
Preventive maintenance and predictive maintenance are two common types of maintenance that manufacturers use to ensure their equipment operates optimally.
Both methods involve regular inspections, testing, and maintenance, but they differ in their approach and objectives.
In this article, I’ll discuss the differences between predictive maintenance and preventive maintenance in machine manufacturing.
Preventive Maintenance
Preventive maintenance is a maintenance approach that involves regularly scheduled maintenance tasks to prevent equipment failure.
The aim of preventive maintenance is to prevent unplanned downtime, reduce repair costs, and extend equipment lifespan.
Preventive maintenance involves regularly inspecting and testing equipment, replacing worn-out parts, and performing routine maintenance tasks such as cleaning, lubrication, and calibration.
Preventive maintenance is based on the concept that equipment has a predictable lifespan, and maintenance tasks can be scheduled based on this lifespan.
For example, if a machine’s bearings are designed to last for 1000 hours of operation, preventive maintenance tasks may include replacing the bearings after every 800 hours of operation.
This approach is based on the assumption that equipment components wear out predictably, and regular maintenance can prevent equipment failure and extend its lifespan.
Advantages of Preventive Maintenance
Some of the advantages of preventive maintenance are:
Reduced downtime
Regular preventive maintenance tasks can prevent equipment failure and reduce downtime.
Extended equipment lifespan
Preventive maintenance can extend the lifespan of equipment and reduce the need for costly replacements.
Improved safety
Preventive maintenance can identify potential safety hazards and prevent accidents.
Disadvantages of preventive maintenance
Some of the disadvantages of preventive maintenance include:
High cost
Preventive maintenance can be expensive, particularly if equipment components are replaced before they reach the end of their lifespan.
Disruption to operations
Preventive maintenance can disrupt production schedules and affect productivity.
Inefficient use of resources
Preventive maintenance tasks may be performed when they are not necessary, leading to inefficient use of resources.
Predictive Maintenance
Predictive maintenance is a maintenance approach that involves using data and analytics to predict equipment failure and schedule maintenance tasks accordingly.
The aim of predictive maintenance is to minimize equipment downtime, reduce maintenance costs, and improve equipment performance.
Predictive maintenance involves collecting data from equipment sensors, analyzing this data using algorithms, and using the insights gained to schedule maintenance tasks.
Predictive maintenance is based on the concept that equipment failure is not random, and there are usually warning signs that can be detected before the equipment fails.
For example, a machine’s temperature may increase before a bearing fails, or its vibration levels may increase before a motor fails.
By monitoring these indicators, predictive maintenance can detect potential equipment failure and schedule maintenance tasks to prevent the failure from occurring.
Advantages of Predictive Maintenance
Some of the advantages of predictive maintenance include:
Reduced downtime
Predictive maintenance can detect potential equipment failure and schedule maintenance tasks before the failure occurs, reducing downtime.
Improved equipment performance
Predictive maintenance can identify performance issues and schedule maintenance tasks to improve equipment performance.
Lower maintenance costs
Predictive maintenance can reduce maintenance costs by minimizing the need for unplanned maintenance and reducing the likelihood of equipment failure.
Disadvantages of Predictive Maintenance
However, some of the disadvantages of predictive maintenance are:
High implementation costs
Predictive maintenance requires specialized sensors and analytics software, which can be expensive to implement.
Complex analytics
Predictive maintenance requires complex algorithms to analyze data accurately, which can be challenging to develop and maintain.
Lack of data
Predictive maintenance relies on data from sensors, and if sensors are not installed or not functioning correctly, the predictive maintenance approach may not be effective.
Predictive maintenance and preventive maintenance have some similarities, but they differ in their approach and objectives.
Predictive Maintenance at MontBlancAI
MontBlancAI firmly believes that predictive maintenance is a more efficient approach to machine maintenance. As such, we have taken steps to address some of the drawbacks associated with this maintenance approach.
High implementation costs
One such drawback is the high implementation costs.
Many manufacturers and operators find the cost of implementing software to monitor machine data to be prohibitively expensive. However, our tool aims to make it more accessible by streamlining the implementation process and reducing costs.
Our tool is designed to be user-friendly and includes a range of features that make it easier for manufacturers and operators to implement predictive maintenance tasks at a lower cost than traditional tools.
Complexity of data analytics
Another of its drawbacks is the complexity of data analytics. Our tool aims to simplify the complex analytics associated with machine manufacturing data. With just a few clicks, users can easily access comprehensive analytics metrics.
Lack of data
Finally, we have found that a common issue with predictive maintenance is not the lack of data, but rather the difficulty in extracting and processing the available data. To address this issue, we partner with companies that make it easy to extract data from machines. Our software then takes care of the complex processing of this data.
In summary, MontBlancAI firmly believes in the efficiency of predictive maintenance and has taken steps to address some of the drawbacks associated with this approach. By streamlining the implementation process, simplifying analytics, and partnering with data extraction companies, we aim to make predictive maintenance more accessible to manufacturers and operators.
More on Predictive Maintenance
A few months ago, I had a chat with a manufacturing professional about predictive maintenance. At that time, she told me she had yet to have come across any software tool that can actually do predictive maintenance.
I tend to agree with her. I’m not sure if our tool (or any other in the market) can do predictive maintenance the way we all think of it.
In a sense, you can view predictive maintenance as one of those aspirational goals that no one will ever quite get to, but that we can/& should all try to closer and closer to, because of all the benefits.
Everything I mentioned above about how we do it at MontBlancAI is a way of getting closer and closer to that ultimate goal.
How to do predictive maintenance at your factory
As I mentioned above, predictive maintenance can be that aspirational goal that we all strive for, but never quite get to. That is important to remember as you embark on your journey to implement predictive maintenance at your factory.
Though you might not be able to quite get there, you can take steps to get closer and closer. The closer you get to it, the more of its benefits you will see on the way. Below are a few things you can do to get you closer to that dream goal.
NOTE: I am adding this part about ‘how to do predictive maintenance’ because predictive maintenance relies a lot more on software than preventive maintenance, and we happen to be software experts.
Step 1: Data, data, data…
Without data (ALOT of it), you will never quite get there (if at all). Because you need a lot of data, it’s important, if not essential, that you consider a strategy for automated data collection. For this, you’re going to have to think of a way to get data directly from your machines to some sore of data storage (preferably the cloud).
Of course, you can collect data the old (hard) way, manually using pen & paper & excel sheets. There are two problems with both of these methods:
- Manual data collection is prone to errors because humans are error-prone.
- Manual data collection is slow. Since one person actually has to look at the data and collect it (on paper or with spreadsheets. Automated data collection is much faster since there is no human between the data generated by the sensors on the machine, and wherever you decide to store it.
Step 2: Analytics Software
Once you have a way to automatically collect data from your machine, you’ll have to find a tool that can help you process that data. Of course our production monitoring tool can help you do that, but the point of this article isn’t to sell you on our capabilities, but rather to help you achieve your goals.
As such below are some resources where you can search for software in manufacturing.
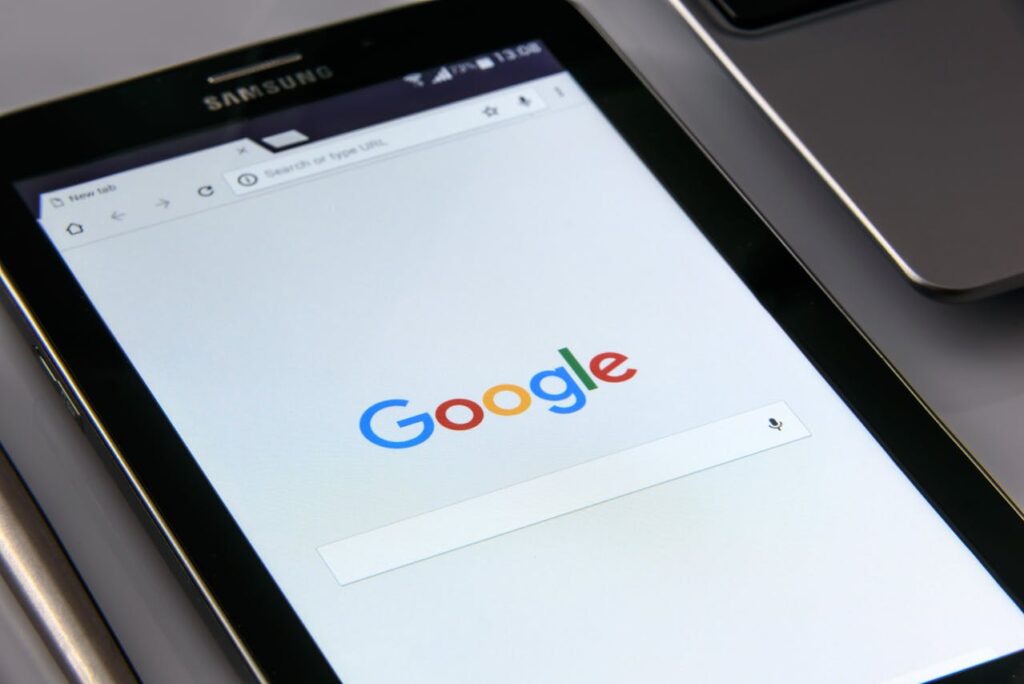
These are all tools you can use to search for manufacturing software.
As you search for manufacturing software, beware that different types of manufacturing software will have different uses. We have written this article to help you choose the type of software that will help you do predictive maintenance at your factory.
For this purpose, you more than likely will need some sore of production monitoring or production tracking software. But feel free to read the article and decide for yourself what works best for your needs.
Step 3: Connect your data to your analytics software
Once you an automated data collection strategy and a software tool to make sense of all of that data, you’ll have to connect the two so you can start monitoring signals from your lines.
For this, you probably will need the help of the software company who made your analytics tool.
Step 4 (optional): Harness the power of Artificial Intelligence (AI)
Finally, after you have your data connected to your analytics software, an additional step will be to make the best of AI.
This step is completely optional as the first three could help you do predictive maintenance, if done right. For this step, the easiest way to harness the power of AI would be to search for a software tool that has AI capabilities.
By following these steps, you can move closer to implementing predictive maintenance at your factory, unlocking incremental benefits along the way.
Conclustion
So, there you have it. The differences between predictive and preventive maintenance, and how to get close to predictive maintenance in 4 simple steps.
Hope the article was helpful. Let us know if we missed anything in the comments.